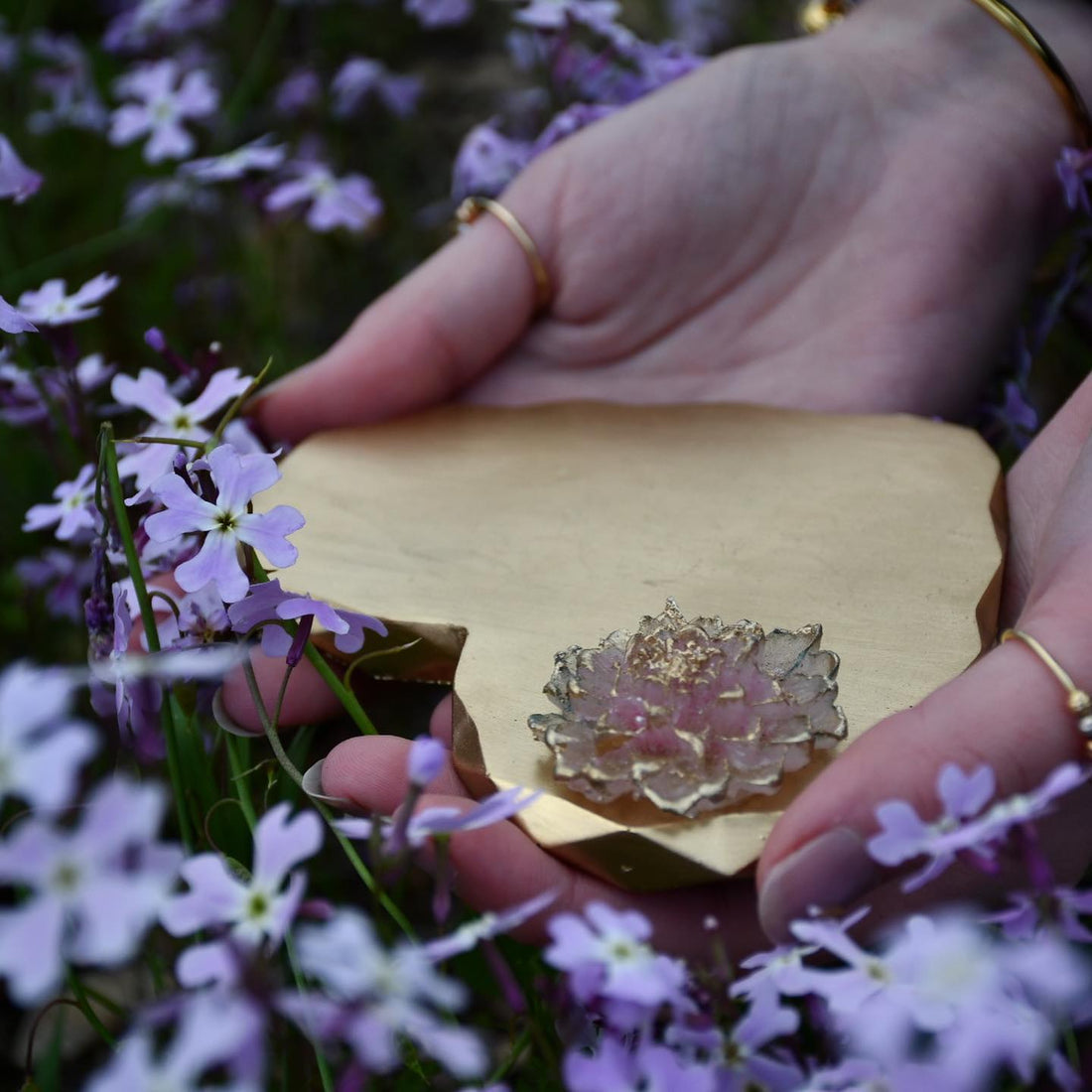
5 Potential Epoxy Problems and How to Avoid Them
Share
To complete an epoxy project, the user/creator proceed through several key phases and sometimes a few optional phases. During each of these phases, there's the potential for mistakes to be made which can affect the resulting epoxy finish.
Reduced clarity, a weaker bond, failed curing, etc., are all potential outcomes of an epoxy project handled incorrectly, even when using a high-quality epoxy like our premium JHKL resin.
In this article, we'll focus on 5 of the most common problems that occur as a result of mistakes made by users during the epoxy process. By being informed of the potential problem and how to avoid it, you'll be better prepared to achieve a perfect, crystal-clear cure in your own epoxy endeavors.
5 common problems that occur when working with epoxy
Among the various things that can go wrong during an epoxy project, there are several that tend to be far more prevalent; below, we'll discuss the following 5 issues:
- Air bubbles
- A cloudy finish
- Yellowing in the epoxy
- A tacky surface or soft spots
- Deep cracks and scratches
Each of these issues has at least one cause that is easily avoided. Let's take a look at them one by one, starting from the top.

Common Problem #1: Air bubbles in the epoxy
Air bubbles are just tiny pockets of air suspended within an epoxy finish, and the presence of air bubbles is by far the most common issue encountered by people working with epoxy.
What causes air bubbles?
Air bubbles have two primary causes:
- Pores in the substrate material.
- Induction during the measuring, mixing, or pouring phases.
Pores in the substrate material
The first is from the substrate material (i.e., the surface that epoxy will be applied to as a sealant). Nearly all suitable substrate materials are porous to some degree. These pores naturally hold air, and when epoxy is applied to the substrate, it seeps into the pores, pushing the air out.
However, because most epoxy is viscous, the air sometimes struggles to make it to the surface where it can release into the environment. If an epoxy layer is too thick and the air fails to surface, it will instead become trapped—suspended within the epoxy resin as an air bubble.
Induction during epoxy batch preparation and application
The second occurs when air is pulled into an epoxy batch while it is being measured, mixed, or poured. Generally, this happens due to excessive force being applied while mixing, either by hand or via the use of a power drill.
As the air gets pulled into the resin, it tends to get stuck within the thick batch. This can also happen when being poured into or out of the container, if the pouring is done haphazardly, though that is much less common.
Avoiding this problem
Fortunately, the presence of air bubbles in your final finish is relatively easy to avoid.
Here's how:
- Always apply an epoxy seal coat to your substrate before applying any other epoxy coatings. This will push the air out preemptively, and the thin seal coat won't be a problem for the air to pass through.
- When mixing, use only stir sticks for batches below a gallon, avoid using too much force. When using a power drill, keep the speed to no more than medium and make sure the bit is deeply submerge before/during activation.
- When pouring, do so deliberately and smoothly from a height of several inches above the surface.
- Air bubbles that do persist can be removed immediately after pouring with a heat gun or blow torch.
Common Problem #2: A Cloudy Epoxy Finish
A cloudy finish is one that has lost its transparency, with a murky or "cloudy" appearance. This issue is less common than air bubbles but can be quite disheartening to encounter.
Thankfully, the causes are well known and so are the ways to avoid them.
What causes a cloudy finish?
A cloudy finishes has several potential causes:
- The presence of moisture—non-epoxy liquids or high humidity.
- Curing outside a suitable temperature range.
- Inadequate mixing.
- Contaminants, such as miscellaneous particles or other substances.
For epoxy to cure properly, it needs to be free of moisture and given a suitable environment.
Though liquids are unlikely source if the epoxy project is being performed in a controlled space, it's still possible for high humidity to induce moisture into the resin.
In fact, the primary cause of moisture in resin is from excessive ambient humidity and temperatures.
For proper curing, epoxy needs an environments with humidity below 60%. A temperature range around 70°F to 80°F is usually a must, with 75°F being the ideal; this range does vary between different epoxy types, with some resins still being viable at higher and lower temperatures.
Avoiding this problem
- Keep non-epoxy liquids away from the workspace to mitigate spills and spatter.
- When working with epoxy, make sure the humidity level is below 60% and the surrounding temperature is within the recommended range for the epoxy you're using. For most epoxies, 75°F is optimal.
- Be sure to mix your epoxy properly. Follow the instructions provided by the makers of the resin you're using.
- Watch our for particles and other contaminants (for instance, sawdust) that can fall and settle into the epoxy while working with it.
Common Problem #3: Yellowing in the Epoxy
Yellowing is a problem that often occurs with aging in unmixed epoxy. It also happens when epoxy is exposed to UV radiation (generally from sunlight).
Epoxy has a shelf life of about 1 year when unopened. Once the bottle has been opened and oxygen introduced, the yellowing process will hasten, reducing the shelf life to about 2 months maximum.
UV radiation, such as from direct sunlight, can also cause epoxy to yellow. This happens gradually over time, though consistent exposure will increase the rate. Providing shade/shelter from the sun and using mica powder pigments in your resin finish can slow or halt the yellowing process.
Avoiding this problem
- Provide your resin finish shade/shelter. This is most important for outdoor epoxy projects that will be otherwise exposed to direct sunlight.
- Don't let your epoxy sit too long in storage. Mix it up and use it during its shelf life for crystal-clear results!
Common Problem #4: A Tacky Epoxy Surface or Soft Spots
Epoxy can sometimes develop a tacky surface while curing. It might even end up with various soft spots in the finish.
Many of the causes are the same as for a cloudy finish:
- Incorrect mixing ratios.
- Inadequate mixing.
- Using old epoxy components.
- Moisture exposure.
These causes have a tendency to prevent the epoxy from fully curing. You can end up with a surface that is entirely tacky or with hard surface that has one or more soft spots throughout.
Avoiding this problem
Fortunately, the causes for this issue can all be avoided in the same ways mentioned earlier:
- Measure your epoxy carefully according to the required components ratio.
- Mix thoroughly. Again, refer to your instructions for precise details.
- Don't use old epoxy components. If your components are over a year old, they'll start to lose their effectiveness (and often will have begun to yellow). Try to acquire new epoxy to use for your project instead.
- Condition your workspace for a low humidity environment. Maintain optimal temperature and humidity to the best of your ability.
Common Problem #5: Deep Cracks or Scratches
The last issue presented in this article is that of deep, visible scratches or cracks in a cured epoxy finish.
The primary cause of this issue is simply mishandling of the finish. Though incredibly durable, epoxy is not completely impervious to physical damage, and excessively rough physical treatment can cause cracking or scratching within the hardened epoxy surface.
Avoiding this problem
This problem is easy to avoid. Don't overburden the epoxy. And be careful not to damage it with heavy impacts, knives, etc. Mostly common sense things.
Epoxy is a low-maintenance sealant. It doesn't require reinforcement, reapplication, or much upkeep at all. Some basic cleaning is enough to keep it in good shape as long as its not being mistreated.

Substandard resin: A universal cause of epoxy problems
Underlying all of these problems is one universally shared potential cause: using subpar epoxy resin.
When choosing an epoxy resin to use for your project, it's important to select one that is reliable, strong, and will cure properly with a clean, clear finish.
These days, it's difficult to sort through the myriad dealers of resin brands with throwaway names and a deceptively low upfront cost. Oftentimes, these "different" dealers are sourced from the same company, offering imported resin that has been produced with compromised quality to provide an attractive price.
That's why buying your epoxy from a credible, reputable dealer is so valuable. Not only do you get peace of mind in knowing that you're getting what you pay for, but you also get the option to seek customer assistance and support after the fact, without being ignored after you've made your purchase.
Have questions? Want advice? Contact us!
If you have any questions about epoxy resin, or if you'd like assistance in planning an epoxy project, please reach out to us at JHKL RESIN—our epoxy experts are ready to assist!